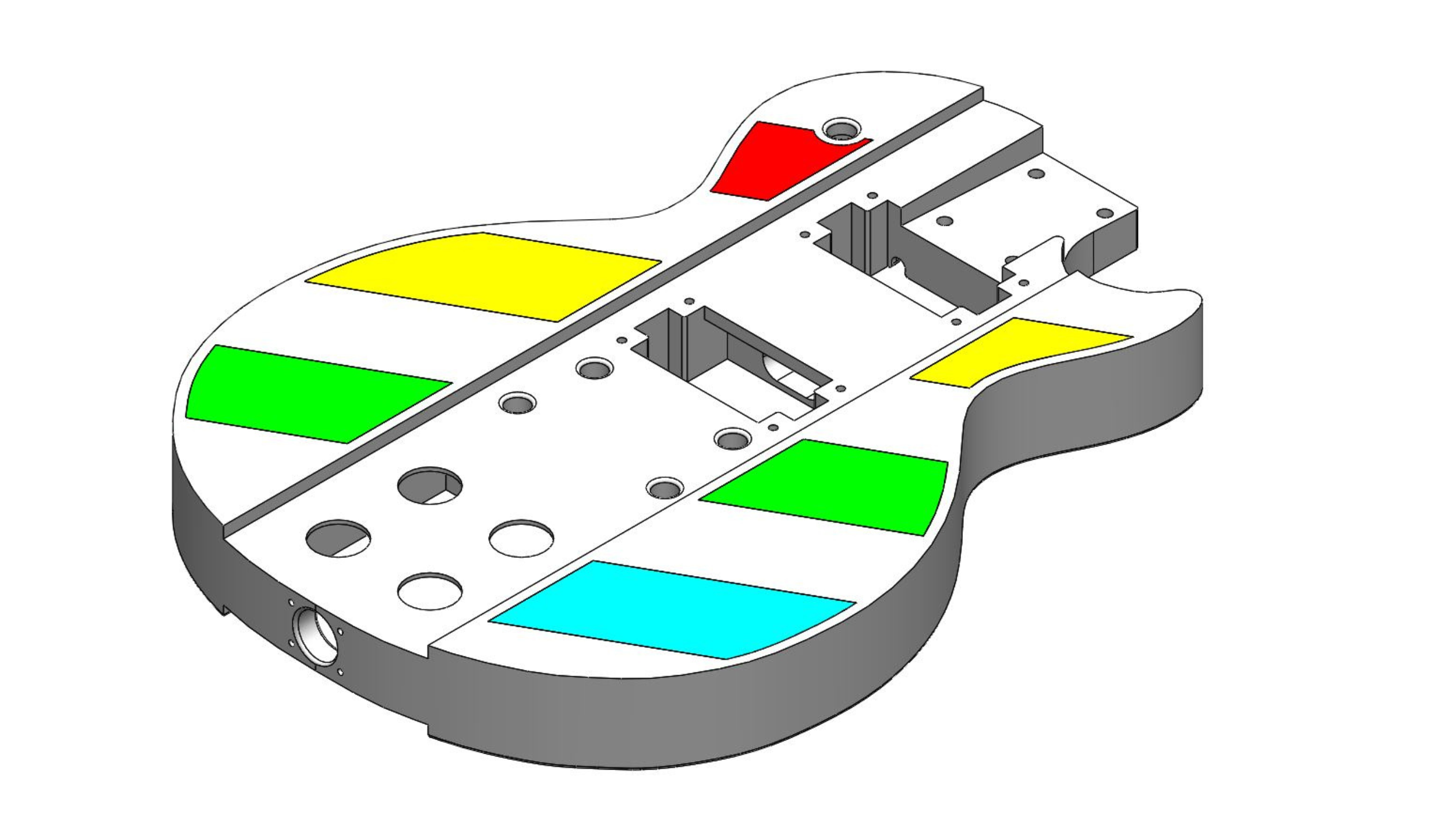
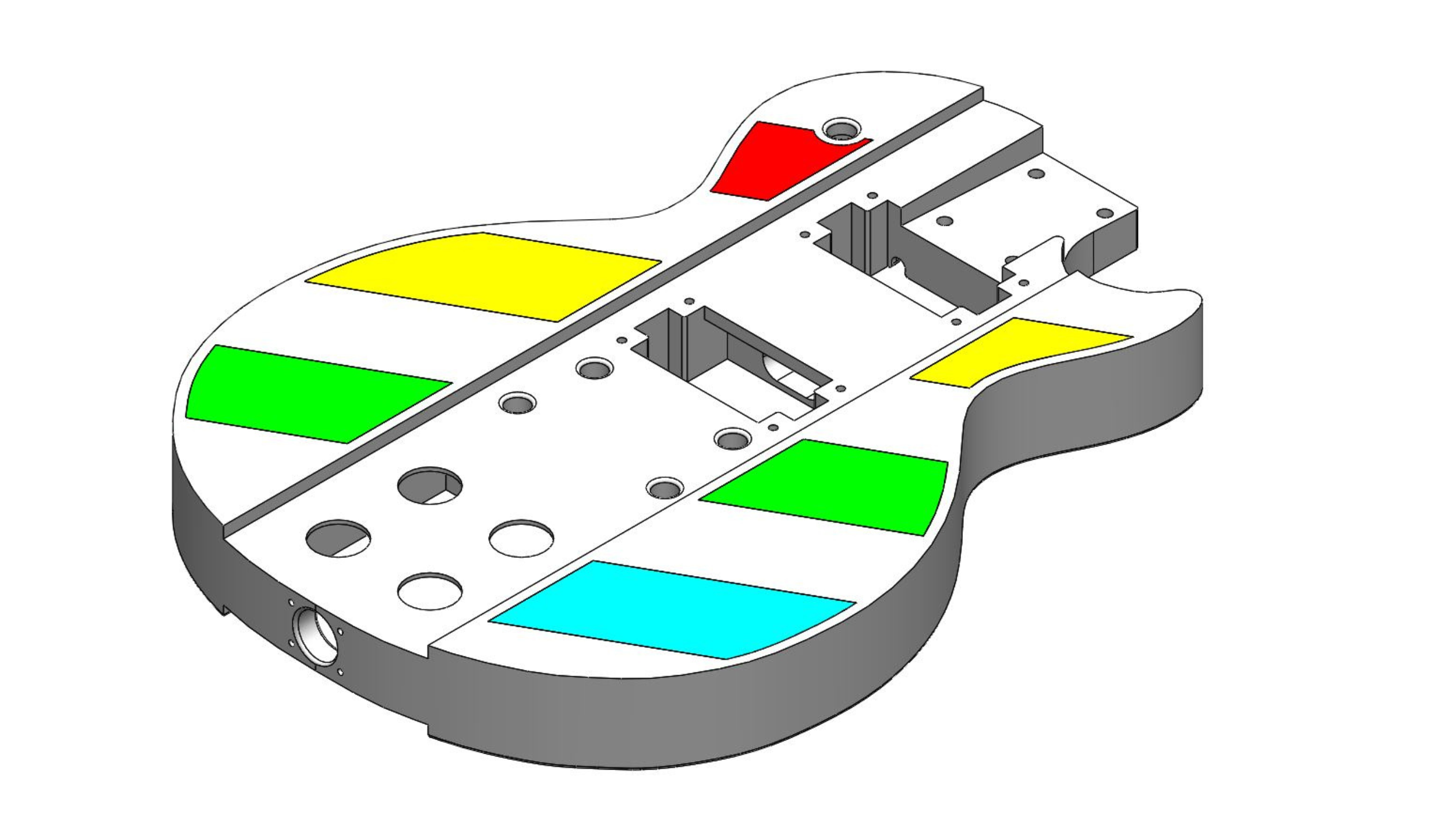
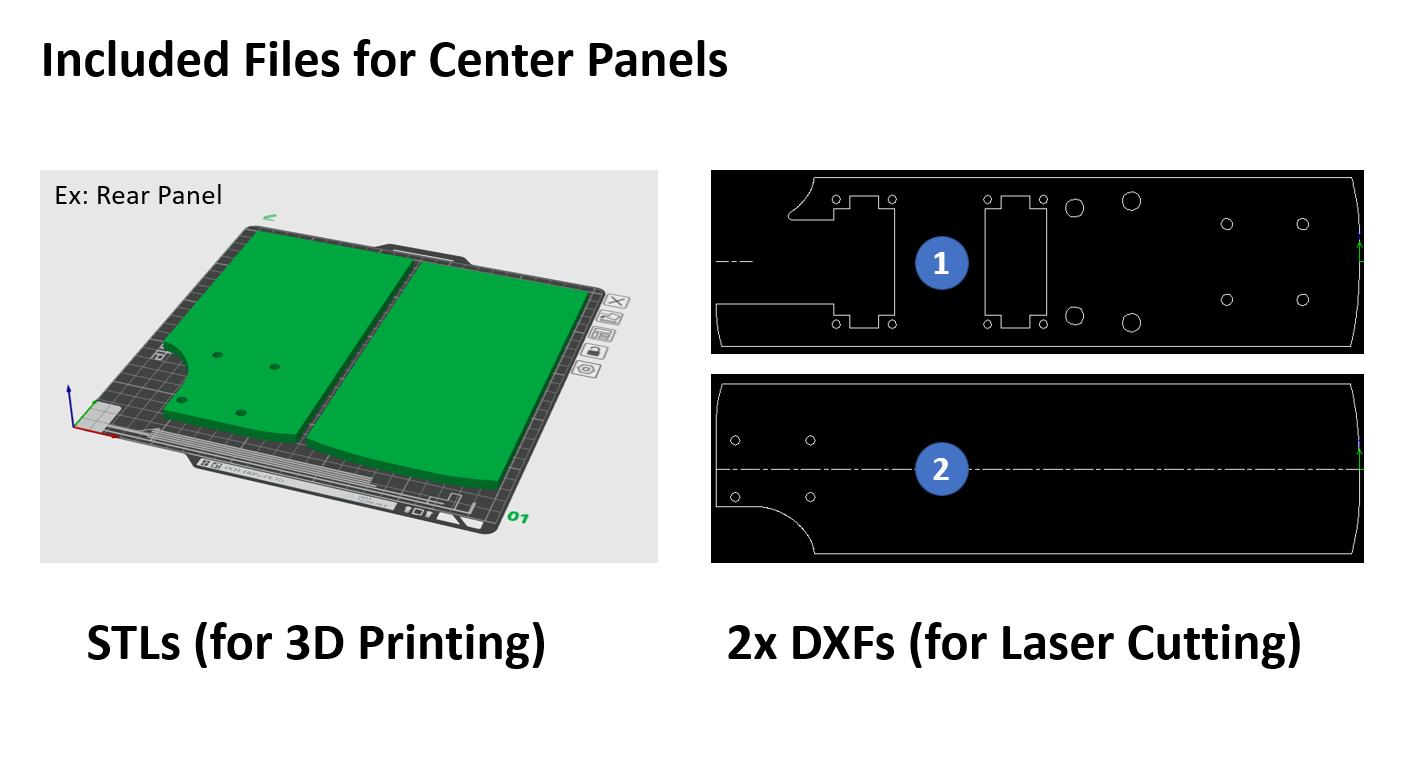
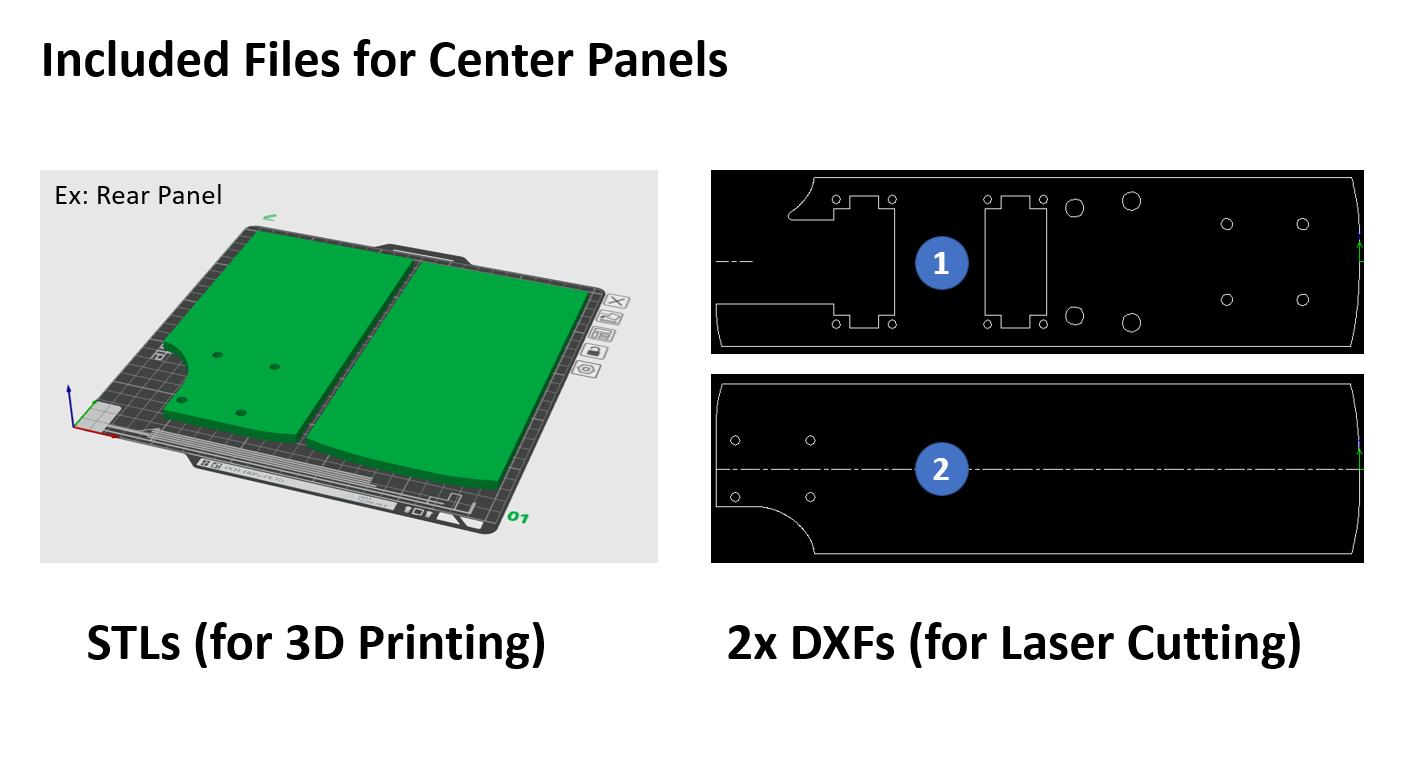
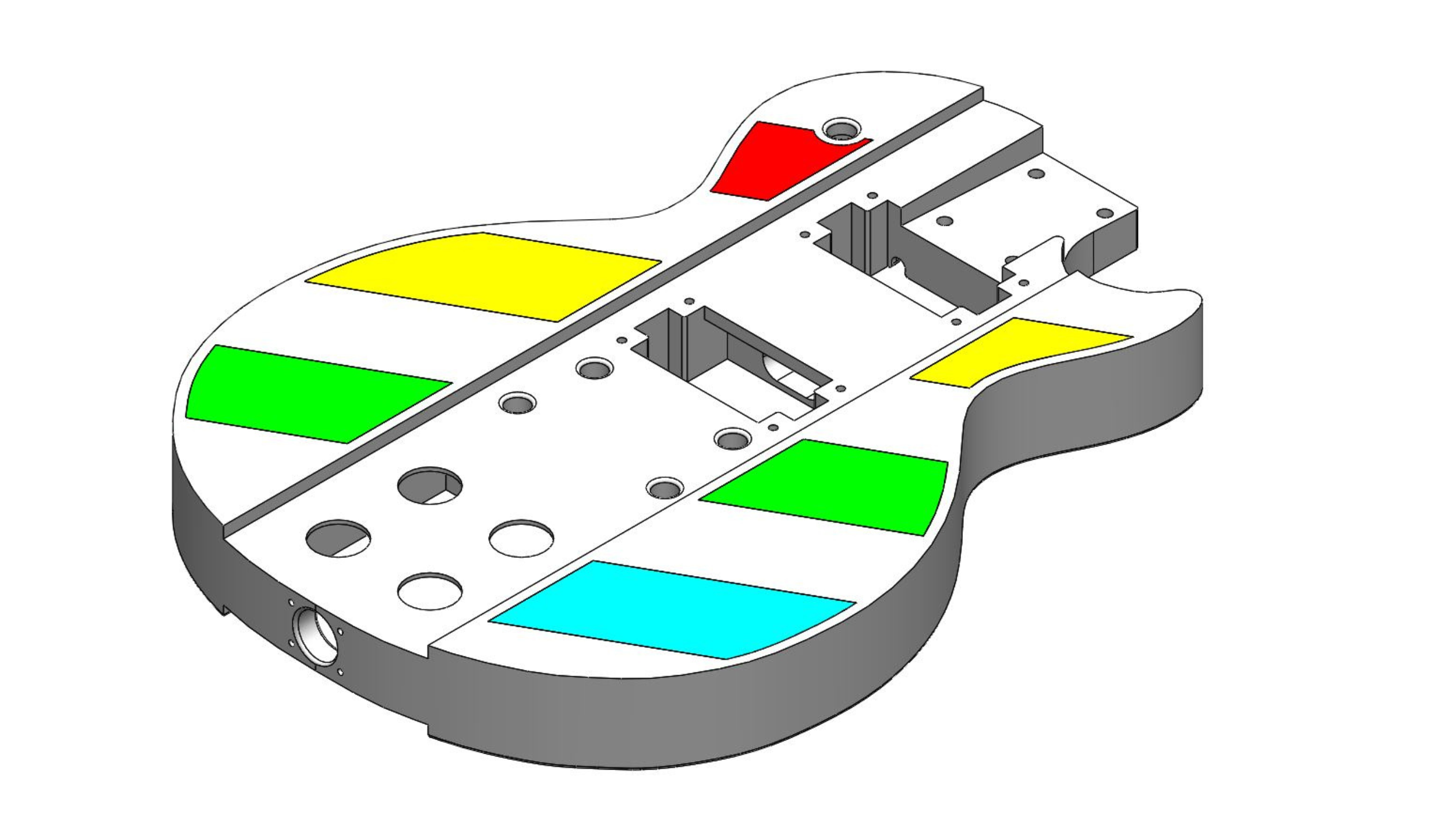
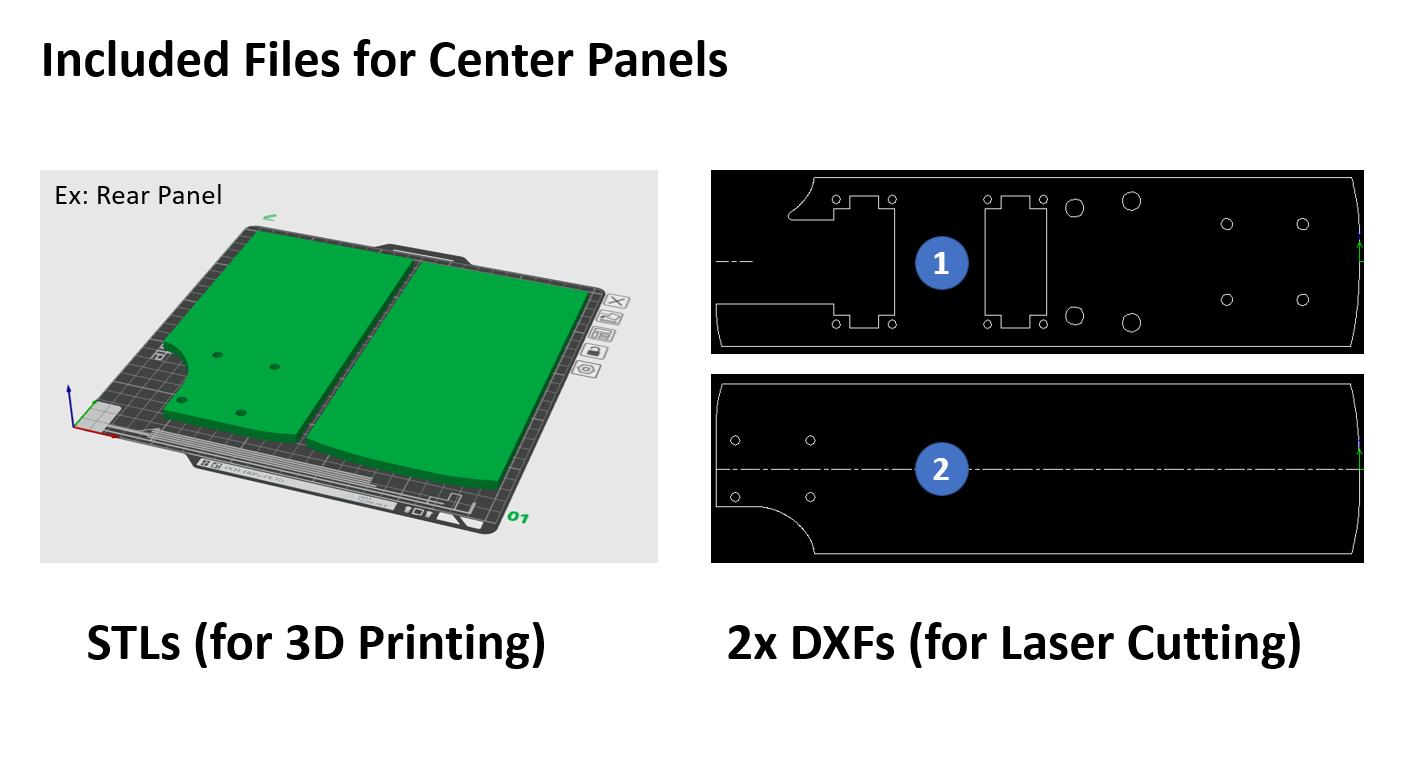
LES PAUL STRIPES
Note: This is a digital download. It includes:
4 STL files of the guitar body in 4 sections
1 STL file of the 3-way switch cover
2 DXF files for laser cutting (1/4” wood) the front and rear center panels
STL files for 3D printing the front and rear center panels (for those who prefer to 3D print the parts)
1 PDF file of the front and rear wood panels
Creative Commons: No commercial use, public sharing, distribution, sale, donation or exchange of the digital files or printed guitar parts/bodies
Check out the project details below for more information on how to build the guitar!
Note: This is a digital download. It includes:
4 STL files of the guitar body in 4 sections
1 STL file of the 3-way switch cover
2 DXF files for laser cutting (1/4” wood) the front and rear center panels
STL files for 3D printing the front and rear center panels (for those who prefer to 3D print the parts)
1 PDF file of the front and rear wood panels
Creative Commons: No commercial use, public sharing, distribution, sale, donation or exchange of the digital files or printed guitar parts/bodies
Check out the project details below for more information on how to build the guitar!
Note: This is a digital download. It includes:
4 STL files of the guitar body in 4 sections
1 STL file of the 3-way switch cover
2 DXF files for laser cutting (1/4” wood) the front and rear center panels
STL files for 3D printing the front and rear center panels (for those who prefer to 3D print the parts)
1 PDF file of the front and rear wood panels
Creative Commons: No commercial use, public sharing, distribution, sale, donation or exchange of the digital files or printed guitar parts/bodies
Check out the project details below for more information on how to build the guitar!
Project Details
Hi everybody and welcome to The 3D Print Zone. So several years back I had this idea to combine two of my hobbies, 3D printing and guitar, and I made my first 3D printed guitar!
I think being able to turn rolls of plastic into functional parts and designs is the core of what makes 3D printing such a powerful tool. And while finding ways to use 3D printers to make functional parts and designs can be more challenging, I think it is way more fun and rewarding in the end.
This is a fun and challenging project and I hope you enjoy the build as much as I did! Check out the build and a demo of the guitar playing here:
☑️ Project Materials ☑️
Affiliate Disclosure: Commissions may be earned on some of the links provided. It won't cost you extra, but will help support the channel!
Filament
Epoxy
Mica Powder
Pickups
Pickup Covers
Tuning Pegs
Neck
Trace Paper
Knobs
Wiring Kit
Neck Plate
Strings
Output Jack
Dowels
Wood Panel
Minwax
PVC Cement
Gorilla Glue
Brass Inserts
Bridge & Tailpiece
3D Printer
http://www.prusa3d.com/#a_aid=the3dprintzone
☑️ 3D Printing ☑️
To print the body of the guitar I split the model into 4 sections so it could be printed on a vast majority of home 3D printers. In my case, I’m printing on a Prusa MK3S+ which has a build area of 210 by 210 mm.
For all of the parts I used the same slicer settings and AmazonBasics White PLA for the filament. I used PrusaSlicer to slice the models with 25% cubic infill. If you are looking for an even stronger and heavier guitar you can certainly increase this value, but keep in mind the print time and amount of filament used will increase quite a bit.
For supports I used Build Plate Only supports to accommodate overhangs and bridging. I found that using 2 perimeters was enough, but you can increase this number if you are looking for additional strength.
Print Speeds
20 mm/s FIRST LAYER
45 mm/s PERIMETERS
80 mm/s INFILL
50 mm/s SUPPORTS
180 mm/s TRAVEL
Print Stats
Top
17.6 hrs Print Time
280 g of Filament
$7.10
Middle
32.1 hrs Print Time
527 g of Filament
$13.37
Left
16.0 hrs Print Time
274 g of Filament
$6.96
Right
16.4 hrs Print Time
286 g of Filament
$7.26
3-Way Switch Cover
0.5 hrs Print Time
6 g of Filament
$0.16
Total
~82 hrs Print Time
1373 g of Filament (~1.4 rolls)
$34.85 (depending on filament brand)
☑️ Body Assembly ☑️
The guitar body is designed to go together using wooden dowel rods. There are 2 purposes for the dowel rods. One, to align the parts during assembly and two, to provide additional stiffness to the 3D printed guitar body. The dowel rods were cut to length using a circular saw and then then edges were sanded down so that they could be inserted into the 3D printed channels easier.
After doing some research online, I decided to use PVC cement to hold the 3D printed sections together because it creates a strong bond as it actually fuses the plastic together. I used a paint brush to coat both the dowel rods and 3D printed contact faces with cement and then pushed the parts together. I used wood clamps to tightly squeeze and hold the parts together to get a strong bond.
There are a few options for adding threads into your 3D printed parts, but I decided to go with brass inserts. To install brass inserts you undersize the hole and can simply press them into position using a soldering iron. This takes a bit of practice so I recommend trying this out on a few test prints before installing them on your 3D printed guitar.
The guitar design has two 1/4 inch poplar wood panels on the top and underside of the guitar. Like the dowel rods, the wood panels are intended to provide additional stiffness to the 3D printed body. To make a stencil for the panels I saved the CAD files a DXF and printed the profiles onto 11 x 17 paper with 100% scaling.
I then used carbon trace paper to transfer the designs to the wood for both the top and bottom panels in order to mark the cut locations for the next step. I used a table saw to rip the panels to the correct width and cut away extra material from the top and bottom to test fit the panels on the printed body.
Next I used a drill to punch out the holes and a jigsaw to cut out the details in the top and bottom panels. For me this was one of the most difficult steps of the build process, and resulted in a few mistakes.
All that to say, if you have access to a laser cutter I would definitely recommend going this route instead to ensure nice clean cuts, even though it is a more expensive option. I ended up just using some wood glue and clamps to re-attached the pieces that snapped off which worked pretty well.
I then used a paint brush to apply Minwax Polycrylic coating to the outer facing surface of the panels. This both protects the wood and gives it a light gloss. In total I ended up applying 4 coats and made sure to sand with 220 sandpaper in between coats.
☑️ Resin Pour ☑️
The next step was my favorite part of the build. I’ve always been fascinated by those awesome epoxy river tables and thought it would be a fun way to both aesthetically give the guitar a unique look, while also serving as another method for increasing the stiffness of the body.
For this step you want to make sure your work surface is as level as possible, as this is critical to ensuring the resin is flat when it cures. I chose a 2-part epoxy made by JB Weld which is a great option because it is clear and rock-solid when it fully cures.
I used the CAD model to calculate the volume of resin needed and determined that both the left and right sections required about 8.3 cubic inches of resin which when added together and converted to mL equals about 270 mL of epoxy. Therefore, I used about 150mL of Part A and 150 mL of Part B to ensure I had enough material with a little extra just in case.
I used Black Diamond Mica powder to give the resin a sparkle-y colorful look to it, choosing Iridescent Blue as the main color, with a bit of Green Envy and Pure White to give it some additional texture and color dynamic.
I chose to mix all of the mica powder in the Part A resin and made sure to mix the powder really well so that it was uniformly distributed. After adding Part B I thoroughly mixed it all together to ensure the epoxy would cure properly. I have to say that I found it super satisfying to pour the resin onto the body and watch it flow into the cavity, and level out.
This step is an opportunity to add your own creativity and really change the overall aesthetic of the design, and for this guitar I decided to give the resin a bit of a textured look by using a wooden stick to create a swirl pattern. There’s really no right or wrong here, I was mainly just going for a semi-random look and overall I am really happy with how it turned out.
One issue I ran into was a small amount of leakage between the seams, so I would recommend first sealing the seams with more PVC cement or coating them with clear epoxy prior to pouring the rest of the resin. I waited 48 hours to let the epoxy full cure and have to say I am extremely happy with how it turned out.
In addition to being nice and level, the resin added a tremendous amount of strength to the body and visually turned out even better than I was expecting. This is something I definitely plan to experiment with more in the future.
I chose to use Gorilla Clear Grip adhesive to attach the front wood panel to the 3D printed body of the guitar. I applied a generous amount of glue to the wood and pressed it into place. I then used wood clamps to hold the panel tightly to the body and let the glue set full 24 hours before removing the clamps.
☑️ Electronics ☑️
Since this is a Les Paul style guitar, for the electronics it requires 2 500k volume knobs, 2 500k tone knobs with capacitors, 2 humbucker pickups, a 3-way switch, and an output jack.
I quickly found that the potentiometer shafts were not long enough, so I had to Dremel away material from the 3D print to allow them to fully extend through the wood so that I could tighten the nut on the other side. Since soldering is not my forte, I decided to purchase a pre-assembled wiring harness to make my life a little easier.
I followed a Seymour Duncan wiring diagram to determine where everything needed to go. There is a cavity for the 3-way switch and a dedicated wire routing channel. It mounts to the body using a nut on the front face of the guitar. Coming off the 3-way switch the red wire was used for the neck and the grey wire was used for the bridge.
There is also a long black wire that has a signal and ground that connects to the output jack. The pickups I used have 4 leads. The black is the hot, the green and bare wire is the ground, and the red and white simply get twisted together and taped off with electrical tape. You will also need to add a few ground wires between the pots as well as one to the bridge to ensure everything is ground properly.
I used M3x10 socket head screws to mount the pickups to the body of the guitar. If you are looking for better quality sound, there is definitely an opportunity to use higher quality electronics for your guitar, but luckily these can be swapped out fairly easily in the future if needed.
I measured the locations to drill holes for the back panel screws and drilled them out. I 3D printed some small spacer rings to cover up any misalignment between the wood panel and guitar body and I used the same Gorilla adhesive to glue the spacers to the Bridge and Tailpiece posts.
I also found that the post fit slightly too loose so I added glue while inserting them into the body. The guitar knobs have small set-screws on the sides and simply get pressed onto the potentiometer shafts and tightened to secure them in place.
The neck is a 22-fret maple neck purchased on Amazon that is black in color to match the guitar hardware. The normal guitar scale for a Les Paul is 24.75 inches so I lined the neck up to the body and measured to make sure the distance from the nut to the 12th fret and the 12th fret to the bridge were both 12 3/8th” and clamped it in place.
I then pre-drilled the location for the neck screws, positioned the neck plate, and bolted the neck to the body of the guitar. Then I installed both the 3-way switch cover and wood back-panel using M3x10 screws.
I had accidently ordered in-line tuning pegs instead of standard tuning pegs but I decided to use them anyways and just installed 3 of them upside-down. Lastly I slid the tailpiece and bridge onto their respective posts, strung up the guitar, and it was finally ready to play! Out of curiosity I weighed the guitar and found that it weighs about 7 lbs 6 ounces which is a bit lighter than a typical Les Paul which ranges from 9 to 12 pounds.
I am really happy with how the guitar came out in the end and I hope you will enjoy the build as much as I did!